Understanding High Power Graphite Electrodes: Key Insights for the Metallurgical and Energy Industries
Summary:
High power graphite electrodes play a crucial role in the metallurgical and energy industries, primarily used in electric arc furnaces (EAFs) for steel production and non-ferrous metal smelting. These electrodes are designed to withstand high electrical currents and temperatures, making them indispensable for efficient metal production.
The manufacturing process of high power graphite electrodes i
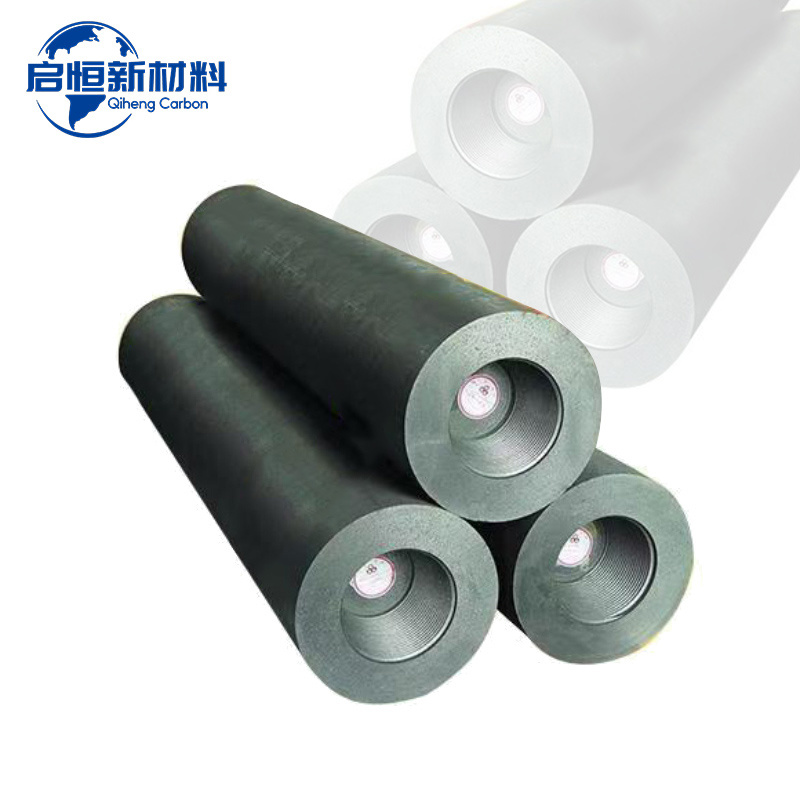
High power graphite electrodes play a crucial role in the metallurgical and energy industries, primarily used in electric arc furnaces (EAFs) for steel production and non-ferrous metal smelting. These electrodes are designed to withstand high electrical currents and temperatures, making them indispensable for efficient metal production.
The manufacturing process of high power graphite electrodes involves several stages. Initially, petroleum needle coke is used as the primary raw material due to its excellent thermal and electrical conductivity properties. This coke is subjected to high temperatures in a carbonization process, transforming it into a graphitic structure. Afterward, the electrodes undergo a series of treatments, including impregnation with pitch and re-baking, to enhance their density and strength. The end result is a product that can endure the rigors of industrial applications.
One of the key advantages of high power graphite electrodes is their ability to conduct electricity with minimal resistance. This attribute is particularly vital in electric arc furnaces, where efficient energy use is essential for maximizing productivity and minimizing operational costs. High power graphite electrodes facilitate higher current loads, which translates to increased melting rates and improved energy efficiency.
In addition to their electrical properties, high power graphite electrodes exhibit excellent thermal conductivity, allowing for effective heat dissipation during the melting process. This characteristic is essential for maintaining optimal operational temperatures and preventing damage to the furnace lining. Moreover, the mechanical strength of these electrodes ensures they can withstand the aggressive conditions within the EAFs, leading to longer operational lifespans and reduced downtime for maintenance.
In recent years, the demand for high power graphite electrodes has risen due to the global push for sustainable steel production. The electric arc furnace method, which relies heavily on these electrodes, is considered more environmentally friendly compared to traditional blast furnace methods. As industries strive for lower carbon footprints, the role of high power graphite electrodes becomes increasingly critical in meeting both production and environmental goals.
Professionals in the metallurgical and energy sectors must stay informed about advancements in high power graphite electrode technology, including innovations in material science and manufacturing techniques. Understanding the unique properties and applications of these electrodes can help industries optimize their processes and enhance their product offerings.
In summary, high power graphite electrodes are essential components in the metallurgical and energy sectors. Their unique properties and advantages make them vital for efficient metal production and sustainable industrial practices. As technology evolves, staying abreast of developments in this field will be crucial for industry professionals seeking to enhance operational efficiency and contribute to eco-friendly initiatives.
The manufacturing process of high power graphite electrodes involves several stages. Initially, petroleum needle coke is used as the primary raw material due to its excellent thermal and electrical conductivity properties. This coke is subjected to high temperatures in a carbonization process, transforming it into a graphitic structure. Afterward, the electrodes undergo a series of treatments, including impregnation with pitch and re-baking, to enhance their density and strength. The end result is a product that can endure the rigors of industrial applications.
One of the key advantages of high power graphite electrodes is their ability to conduct electricity with minimal resistance. This attribute is particularly vital in electric arc furnaces, where efficient energy use is essential for maximizing productivity and minimizing operational costs. High power graphite electrodes facilitate higher current loads, which translates to increased melting rates and improved energy efficiency.
In addition to their electrical properties, high power graphite electrodes exhibit excellent thermal conductivity, allowing for effective heat dissipation during the melting process. This characteristic is essential for maintaining optimal operational temperatures and preventing damage to the furnace lining. Moreover, the mechanical strength of these electrodes ensures they can withstand the aggressive conditions within the EAFs, leading to longer operational lifespans and reduced downtime for maintenance.
In recent years, the demand for high power graphite electrodes has risen due to the global push for sustainable steel production. The electric arc furnace method, which relies heavily on these electrodes, is considered more environmentally friendly compared to traditional blast furnace methods. As industries strive for lower carbon footprints, the role of high power graphite electrodes becomes increasingly critical in meeting both production and environmental goals.
Professionals in the metallurgical and energy sectors must stay informed about advancements in high power graphite electrode technology, including innovations in material science and manufacturing techniques. Understanding the unique properties and applications of these electrodes can help industries optimize their processes and enhance their product offerings.
In summary, high power graphite electrodes are essential components in the metallurgical and energy sectors. Their unique properties and advantages make them vital for efficient metal production and sustainable industrial practices. As technology evolves, staying abreast of developments in this field will be crucial for industry professionals seeking to enhance operational efficiency and contribute to eco-friendly initiatives.
Focus On Hot Spots
Understanding the Lifecycle of a Graphite Crucible: From Creation to Application
Understanding the Lifecycle of a Graphite Crucible
Graphite crucibles are essential tools widely used in various industrial applications, particularly in metallurgy. Their unique properties, such as high thermal conductivity and resistance to thermal shock, make them indispensable for melting metals and other applications. In this article, we will delve into the lifecycle of a graphite crucible, e
Understanding Calcined Petroleum Coke: Properties, Applications, and Benefits
Calcined petroleum coke (CPC) is a carbonaceous solid material derived from the thermal processing of green petroleum coke, which is produced during the oil refining process. The calcination process involves heating green petroleum coke to high temperatures (approximately 1200°C to 1400°C) in a controlled atmosphere, which drives off volatile compounds and enhances the carbon content, resulting in