The Essential Role of Graphite Electrode Carbon Bricks in Metallurgy
Summary:
Graphite electrode carbon bricks are critical components in the metallurgy industry, particularly in processes that require high thermal and electrical conductivity. These bricks are primarily composed of graphite, a form of carbon known for its stability and resistance to thermal shock. Their unique properties make them ideal for use in electric arc furnaces and other applications where high temp
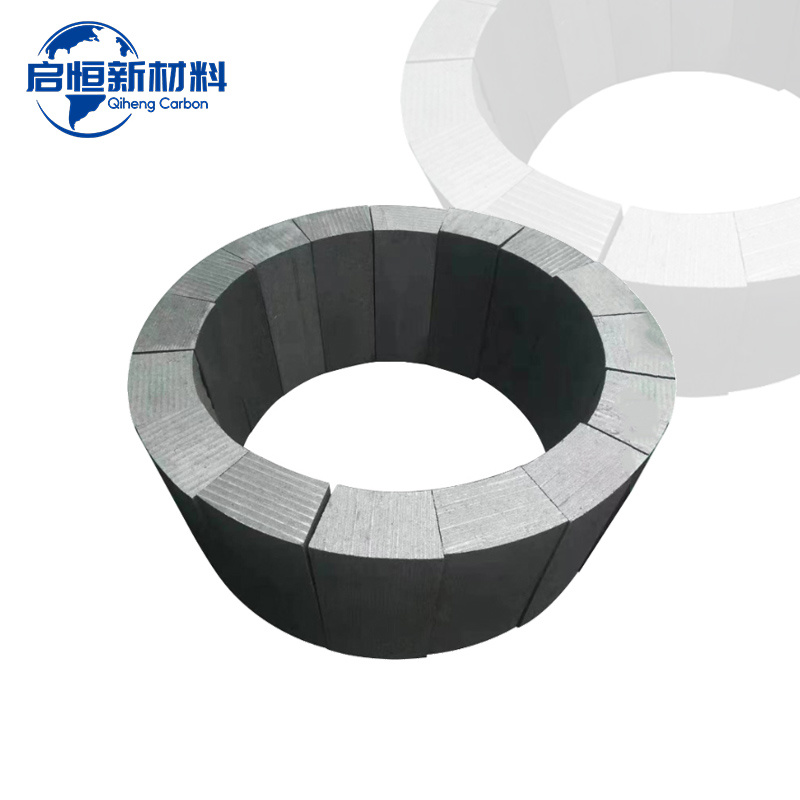
Graphite electrode carbon bricks are critical components in the metallurgy industry, particularly in processes that require high thermal and electrical conductivity. These bricks are primarily composed of graphite, a form of carbon known for its stability and resistance to thermal shock. Their unique properties make them ideal for use in electric arc furnaces and other applications where high temperatures and electrical currents are prevalent.
One of the defining characteristics of graphite electrode carbon bricks is their ability to withstand extreme conditions. When subjected to high temperatures, these bricks maintain structural integrity, thereby enhancing the longevity of the equipment they are used in. This durability is essential in reducing downtime and maintenance costs in industrial operations. Additionally, the thermal conductivity of graphite allows for efficient heat transfer, which is crucial in processes such as steel production and refining metals.
In the production of steel, for instance, graphite electrode carbon bricks play a pivotal role in the functioning of electric arc furnaces. The electrodes, made from these bricks, generate the intense heat required to melt scrap metal, facilitating the recycling process. Their high electrical conductivity ensures that the electric current flows smoothly, maximizing energy efficiency during operation. This not only optimizes production but also minimizes energy consumption, which is a significant concern in today’s industrial landscape.
Moreover, the chemical properties of graphite electrode carbon bricks make them resistant to oxidation and corrosion, further extending their service life in harsh environments. This resilience is particularly beneficial in metallurgical applications, where exposure to various chemicals can be detrimental to other materials. The stability of graphite in these conditions ensures consistent performance over time.
The versatility of graphite electrode carbon bricks extends beyond traditional metallurgical applications. They are also utilized in various energy-related sectors, including battery production and renewable energy systems. Their ability to conduct electricity efficiently makes them suitable for use in advanced energy storage solutions.
In summary, graphite electrode carbon bricks are indispensable in the metallurgy and energy industries due to their exceptional thermal and electrical properties. Their use leads to improved efficiency, reduced operational costs, and enhanced performance in high-temperature applications. As industries continue to evolve, the relevance of these materials remains strong, solidifying their role in modern technological advancements and sustainable practices.
One of the defining characteristics of graphite electrode carbon bricks is their ability to withstand extreme conditions. When subjected to high temperatures, these bricks maintain structural integrity, thereby enhancing the longevity of the equipment they are used in. This durability is essential in reducing downtime and maintenance costs in industrial operations. Additionally, the thermal conductivity of graphite allows for efficient heat transfer, which is crucial in processes such as steel production and refining metals.
In the production of steel, for instance, graphite electrode carbon bricks play a pivotal role in the functioning of electric arc furnaces. The electrodes, made from these bricks, generate the intense heat required to melt scrap metal, facilitating the recycling process. Their high electrical conductivity ensures that the electric current flows smoothly, maximizing energy efficiency during operation. This not only optimizes production but also minimizes energy consumption, which is a significant concern in today’s industrial landscape.
Moreover, the chemical properties of graphite electrode carbon bricks make them resistant to oxidation and corrosion, further extending their service life in harsh environments. This resilience is particularly beneficial in metallurgical applications, where exposure to various chemicals can be detrimental to other materials. The stability of graphite in these conditions ensures consistent performance over time.
The versatility of graphite electrode carbon bricks extends beyond traditional metallurgical applications. They are also utilized in various energy-related sectors, including battery production and renewable energy systems. Their ability to conduct electricity efficiently makes them suitable for use in advanced energy storage solutions.
In summary, graphite electrode carbon bricks are indispensable in the metallurgy and energy industries due to their exceptional thermal and electrical properties. Their use leads to improved efficiency, reduced operational costs, and enhanced performance in high-temperature applications. As industries continue to evolve, the relevance of these materials remains strong, solidifying their role in modern technological advancements and sustainable practices.
Focus On Hot Spots
Understanding the Lifecycle of a Graphite Crucible: From Creation to Application
Understanding the Lifecycle of a Graphite Crucible
Graphite crucibles are essential tools widely used in various industrial applications, particularly in metallurgy. Their unique properties, such as high thermal conductivity and resistance to thermal shock, make them indispensable for melting metals and other applications. In this article, we will delve into the lifecycle of a graphite crucible, e
Understanding Calcined Petroleum Coke: Properties, Applications, and Benefits
Calcined petroleum coke (CPC) is a carbonaceous solid material derived from the thermal processing of green petroleum coke, which is produced during the oil refining process. The calcination process involves heating green petroleum coke to high temperatures (approximately 1200°C to 1400°C) in a controlled atmosphere, which drives off volatile compounds and enhances the carbon content, resulting in