Innovations in Carbon Graphite Electrodes: What You Need to Know
Summary:
Innovations in Carbon Graphite Electrodes: What You Need to Know
Table of Contents
1. Introduction to Carbon Graphite Electrodes
2. Importance of Carbon Graphite Electrodes in Industry
3. Latest Innovations in Carbon Graphite Electrodes
4. Manufacturing Process of Carbon Graphite Electrodes
5. Applications of Carbon Graphite Electrodes
6. Advantages of Using Carbon Graphit
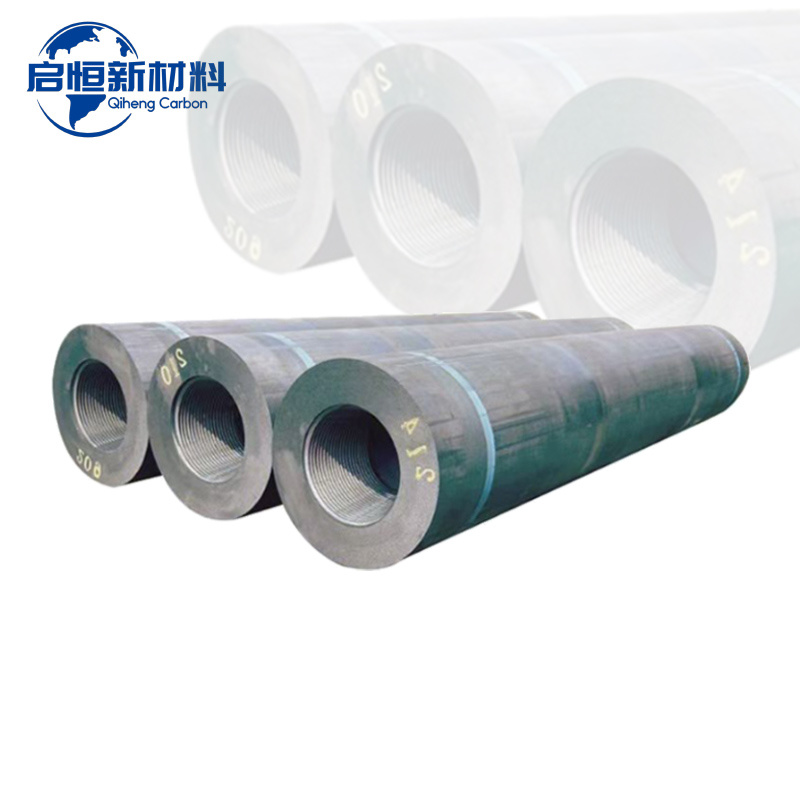
Innovations in Carbon Graphite Electrodes: What You Need to Know
Table of Contents
- 1. Introduction to Carbon Graphite Electrodes
- 2. Importance of Carbon Graphite Electrodes in Industry
- 3. Latest Innovations in Carbon Graphite Electrodes
- 4. Manufacturing Process of Carbon Graphite Electrodes
- 5. Applications of Carbon Graphite Electrodes
- 6. Advantages of Using Carbon Graphite Electrodes
- 7. Environmental Impact and Sustainability
- 8. Future Trends in Carbon Graphite Technology
- 9. Frequently Asked Questions
- 10. Conclusion
1. Introduction to Carbon Graphite Electrodes
Carbon graphite electrodes play a crucial role in various industrial applications, particularly in metallurgy and energy production. These electrodes are primarily used in electric arc furnaces (EAF) for steelmaking, as well as in other sectors like aluminum production and silicon metal manufacturing. The unique properties of carbon graphite, such as high electrical conductivity, thermal resistance, and mechanical strength, make them indispensable in these processes.
As industries evolve, so does the technology behind carbon graphite electrodes. Recent innovations are aimed at enhancing performance, sustainability, and efficiency. Understanding these advancements is vital for professionals in metallurgy and energy sectors to stay competitive and informed.
2. Importance of Carbon Graphite Electrodes in Industry
The significance of carbon graphite electrodes extends beyond their basic functionality. They are the backbone of many essential processes:
- **Energy Efficiency**: Utilizing high-quality electrodes can lead to lower energy consumption in electric arc furnaces, which is increasingly important as industries aim to reduce their carbon footprint.
- **Quality of End Products**: The integrity of the electrodes directly affects the quality of the produced steel and other metals. Innovations in electrode design and materials contribute to stronger, purer end products.
- **Cost-Effectiveness**: Advances in the manufacturing process can lead to reduced production costs, benefiting both producers and consumers.
The interplay of these factors emphasizes the need for continuous innovation in carbon graphite electrodes.
3. Latest Innovations in Carbon Graphite Electrodes
Recent trends in carbon graphite electrode technology showcase a focus on improving both the material properties and the manufacturing processes. Key innovations include:
3.1 Enhanced Material Composition
New formulations of carbon graphite electrodes, including the incorporation of advanced additives, improve electrical conductivity and thermal stability. This results in longer-lasting electrodes that can withstand higher operational temperatures.
3.2 Improved Manufacturing Techniques
The adoption of modern manufacturing techniques, such as isostatic pressing and advanced baking technologies, allows for the production of electrodes with fewer defects and more uniform properties. These processes ensure higher durability and performance consistency.
3.3 Smart Technologies
The integration of smart technologies, including sensors and IoT devices, enables real-time monitoring of electrode performance. This innovation allows for predictive maintenance, minimizing downtime and enhancing overall efficiency in production processes.
3.4 Eco-Friendly Alternatives
With sustainability becoming a crucial concern, research into eco-friendly materials and production processes is on the rise. Innovations aimed at reducing the environmental impact of electrode manufacturing are gaining traction, including the use of renewable resources and less harmful chemicals.
4. Manufacturing Process of Carbon Graphite Electrodes
The manufacturing process of carbon graphite electrodes involves several key stages:
4.1 Raw Material Selection
High-quality petroleum and needle cokes serve as the primary raw materials. The choice of materials significantly influences the final product's properties.
4.2 Mixing and Molding
The raw materials are mixed with various binding agents and molded into the desired shape. This stage often utilizes advanced techniques to ensure uniformity.
4.4 Baking and Graphitization
The molded electrodes undergo a baking process at high temperatures, followed by graphitization, which converts the carbon into a more crystalline form and enhances conductivity.
4.5 Machining and Quality Control
After baking, the electrodes are machined to precise dimensions. Rigorous quality control measures are implemented to ensure that each batch meets the required standards.
5. Applications of Carbon Graphite Electrodes
Carbon graphite electrodes are vital across various industries:
5.1 Steel Production
In electric arc furnaces, carbon graphite electrodes conduct electricity to melt scrap steel. Their performance directly influences the efficiency and quality of steel production.
5.2 Aluminum Production
These electrodes are also used in aluminum smelting processes, facilitating the electrochemical reactions required for aluminum extraction.
5.3 Silicon Metal Production
In silicon production, carbon graphite electrodes are essential for conducting electricity in the reduction of silica, a crucial step in the manufacturing of silicon alloys.
5.4 Other Specialized Applications
Emerging applications include their use in the manufacturing of battery materials and in various electronic components, highlighting the versatility and expanding role of carbon graphite electrodes in modern technology.
6. Advantages of Using Carbon Graphite Electrodes
The benefits of carbon graphite electrodes are manifold:
6.1 High Electrical Conductivity
The superior electrical conductivity of carbon graphite allows for efficient energy transfer, which is critical in high-temperature industrial processes.
6.2 Thermal Stability
Their ability to withstand extreme temperatures without degrading ensures reliability in demanding applications, which is vital in maintaining productivity.
6.3 Mechanical Strength
High mechanical strength protects against breakage and wear, leading to longer service life and reduced operational costs.
6.4 Versatility
Their adaptability to various applications makes them a preferred choice across multiple sectors, from metallurgy to electronics.
7. Environmental Impact and Sustainability
With growing environmental concerns, the carbon graphite electrode industry is taking steps toward sustainability:
7.1 Reducing Carbon Footprint
Innovations aimed at reducing carbon emissions during the manufacturing process are becoming a priority. This includes optimizing energy use and exploring alternative materials.
7.2 Recycling Initiatives
There is an increasing focus on recycling used electrodes and repurposing materials, contributing to a circular economy and minimizing waste.
7.3 Compliance and Regulations
Manufacturers are adapting to stricter environmental regulations, ensuring that production processes comply with both local and international standards.
8. Future Trends in Carbon Graphite Technology
As the industry progresses, several trends are expected to shape the future of carbon graphite electrodes:
8.1 Advanced Material Research
Ongoing research into new composite materials promises to enhance the performance characteristics of electrodes, making them even more efficient and durable.
8.2 Digital Transformation
The integration of AI and machine learning in manufacturing processes will enable smarter production techniques and predictive maintenance strategies, leading to improved efficiency.
8.3 Global Market Trends
As demand for steel and aluminum rises in developing economies, the carbon graphite electrode market is poised for significant growth. Companies that invest in innovative technologies and sustainability practices will have a competitive advantage.
9. Frequently Asked Questions
9.1 What are carbon graphite electrodes made of?
Carbon graphite electrodes are primarily made from high-quality petroleum and needle cokes, which are carbon-rich materials. These materials are processed through mixing, molding, and baking to create the final product.
9.2 How do carbon graphite electrodes work?
These electrodes conduct electricity and are used in electric arc furnaces to melt metal scrap. The electrical current generates heat, enabling the melting process essential for steel and aluminum production.
9.3 What industries use carbon graphite electrodes?
Carbon graphite electrodes are widely used in steel production, aluminum smelting, silicon metal production, and emerging applications in electronics and battery manufacturing.
9.4 What are the advantages of carbon graphite electrodes over other materials?
Carbon graphite electrodes offer superior electrical conductivity, thermal stability, mechanical strength, and versatility compared to alternative materials, making them ideal for high-performance applications.
9.5 How is the environmental impact of carbon graphite electrode production being addressed?
The industry is focusing on reducing carbon emissions, enhancing recycling initiatives, and complying with environmental regulations to minimize the ecological footprint of electrode production.
10. Conclusion
Carbon graphite electrodes are at the forefront of technological advancements in metallurgy and energy production. Innovations in material composition, manufacturing processes, and smart technologies are shaping the future of these essential components. As industries strive for greater efficiency and sustainability, understanding and adopting these advancements will be crucial for staying competitive. By embracing innovations and addressing environmental challenges, the carbon graphite electrode industry can pave the way for a more sustainable and efficient future.
Focus On Hot Spots
Understanding the Lifecycle of a Graphite Crucible: From Creation to Application
Understanding the Lifecycle of a Graphite Crucible
Graphite crucibles are essential tools widely used in various industrial applications, particularly in metallurgy. Their unique properties, such as high thermal conductivity and resistance to thermal shock, make them indispensable for melting metals and other applications. In this article, we will delve into the lifecycle of a graphite crucible, e
Understanding Calcined Petroleum Coke: Properties, Applications, and Benefits
Calcined petroleum coke (CPC) is a carbonaceous solid material derived from the thermal processing of green petroleum coke, which is produced during the oil refining process. The calcination process involves heating green petroleum coke to high temperatures (approximately 1200°C to 1400°C) in a controlled atmosphere, which drives off volatile compounds and enhances the carbon content, resulting in