The Future of Metallurgical Industries with RP Graphite Electrodes: Innovations and Insights
Summary:
The Future of Metallurgical Industries with RP Graphite Electrodes
Table of Contents
1. Introduction to RP Graphite Electrodes
2. The Role of RP Graphite Electrodes in Metallurgy
3. Advantages of Using RP Graphite Electrodes
4. Applications in the Metallurgical Sector
5. Future Trends in RP Graphite Electrodes
6. Environmental Impact and Sustainability
7. Challenges Facing the Indus
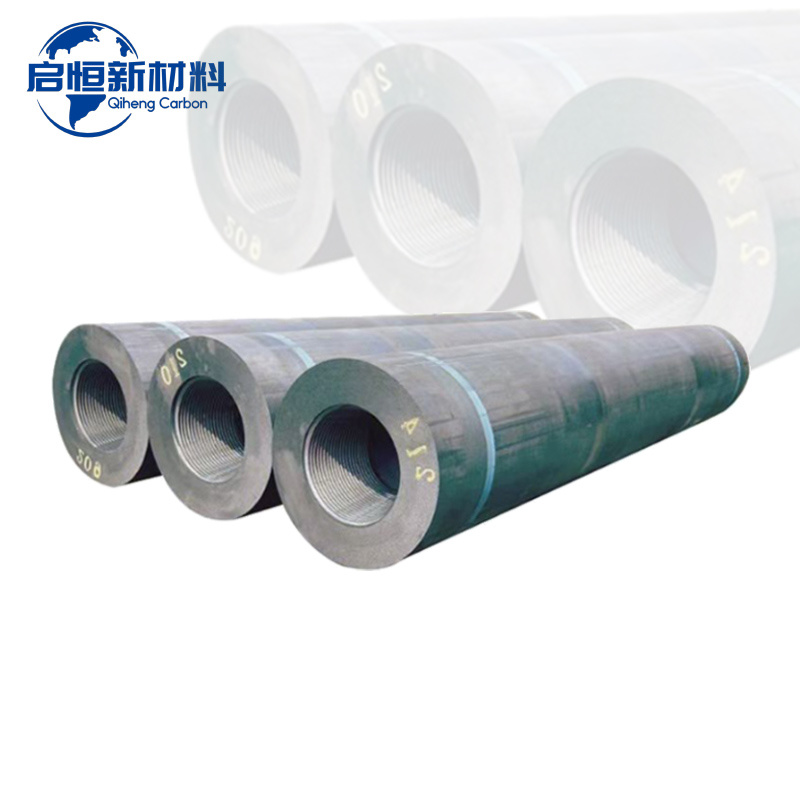
The Future of Metallurgical Industries with RP Graphite Electrodes
Table of Contents
- 1. Introduction to RP Graphite Electrodes
- 2. The Role of RP Graphite Electrodes in Metallurgy
- 3. Advantages of Using RP Graphite Electrodes
- 4. Applications in the Metallurgical Sector
- 5. Future Trends in RP Graphite Electrodes
- 6. Environmental Impact and Sustainability
- 7. Challenges Facing the Industry
- 8. Frequently Asked Questions
- 9. Conclusion
1. Introduction to RP Graphite Electrodes
RP graphite electrodes, or Regular Power graphite electrodes, play a pivotal role in the metallurgical industries, especially in electric arc furnaces (EAF) used for steelmaking. These electrodes are known for their excellent conductivity and ability to withstand high temperatures, making them integral to various metallurgical processes. As industries evolve, the adoption of RP graphite electrodes is reshaping production methods, enhancing efficiency, and paving the way for innovative practices.
2. The Role of RP Graphite Electrodes in Metallurgy
In the metallurgical sphere, RP graphite electrodes serve as a critical component in electric arc furnaces. These electrodes facilitate the melting of scrap steel and other metals through the application of electric current. The process harnesses the thermal energy generated, leading to efficient metallurgical reactions. Additionally, RP graphite electrodes are instrumental in various applications beyond steel production, including the manufacturing of ferroalloys and non-ferrous metals.
Key Functions of RP Graphite Electrodes
- **Electric Conductivity**: They possess superior electrical conductivity, crucial for efficient melting processes.
- **Thermal Stability**: Their ability to withstand extreme temperatures ensures durability during operation.
- **Chemical Resistance**: RP graphite electrodes exhibit resistance to oxidation and corrosion, prolonging their lifespan.
3. Advantages of Using RP Graphite Electrodes
The advantages of RP graphite electrodes extend beyond basic functionality; they significantly enhance metallurgical processes.
Enhanced Efficiency
The use of RP graphite electrodes increases the efficiency of electric arc furnaces, allowing for faster melting times and reduced energy consumption. This efficiency translates to lower production costs, making it an attractive option for manufacturers.
Cost-Effectiveness
While the initial investment in RP graphite electrodes may be substantial, the long-term savings on energy and maintenance make them cost-effective. Their durability reduces the frequency of replacements, further contributing to lower operational costs.
Versatility in Applications
RP graphite electrodes can be utilized across various industries, from steelmaking to non-ferrous metal production. This versatility enhances their appeal to manufacturers seeking flexibility in their operations.
4. Applications in the Metallurgical Sector
RP graphite electrodes find diverse applications within the metallurgical sector. The most notable application is in electric arc furnaces, but their utility extends to several other domains.
Electric Arc Furnaces
In electric arc furnaces, RP graphite electrodes are essential for melting scrap steel. The high temperatures generated facilitate efficient metallurgical reactions, essential for producing high-quality steel.
Ferroalloy Production
Ferroalloys, such as ferrosilicon and ferromanganese, are produced using RP graphite electrodes in submerged arc furnaces. These ferroalloys are crucial for steel production, enhancing the material's properties.
Non-Ferrous Metal Production
RP graphite electrodes are also employed in the production of non-ferrous metals, such as aluminum and copper, where their high conductivity and thermal stability are advantageous.
5. Future Trends in RP Graphite Electrodes
The metallurgical industry is witnessing rapid advancements, and RP graphite electrodes are at the forefront of these changes. Future trends indicate significant transformations.
Technological Innovations
Emerging technologies, such as artificial intelligence and IoT, are being integrated into electrode production and utilization. These innovations promise to improve the performance and monitoring of RP graphite electrodes in real-time.
Sustainability Initiatives
As industries move towards more sustainable practices, the demand for eco-friendly solutions is rising. RP graphite electrodes, with their potential for recycling and reduced energy consumption, position themselves as a sustainable choice for the future.
Customization for Specific Industries
The future may see an increase in the customization of RP graphite electrodes tailored to specific industrial needs. This bespoke approach can enhance performance and efficiency in various applications, benefiting manufacturers.
6. Environmental Impact and Sustainability
Sustainability in the metallurgical industry is becoming increasingly important as environmental concerns grow. RP graphite electrodes contribute positively to these efforts.
Lower Carbon Footprint
Using RP graphite electrodes can significantly reduce the carbon footprint of metallurgical processes. Their efficiency in energy consumption leads to lower greenhouse gas emissions, aligning with global sustainability goals.
Recyclability
RP graphite electrodes can be recycled at the end of their lifecycle, contributing to a circular economy. This characteristic makes them a more sustainable choice compared to other materials that may not be recyclable.
Compliance with Environmental Regulations
The metallurgy sector is subject to stringent environmental regulations. The adoption of RP graphite electrodes helps manufacturers comply with these regulations, promoting responsible production practices.
7. Challenges Facing the Industry
Despite the numerous advantages of RP graphite electrodes, the industry faces several challenges that must be addressed.
Supply Chain Issues
The global supply chain for raw materials used in RP graphite electrodes can be volatile. Disruptions in the supply chain may affect production consistency, leading to challenges in meeting demand.
Technological Adaptation
As new technologies emerge, industries must navigate the adaptation process. Investing in advanced technologies to optimize the use of RP graphite electrodes requires substantial resources and training.
Market Competition
The metallurgical market is highly competitive, with various alternatives available for producers. RP graphite electrodes must continually demonstrate their value proposition to maintain market share.
8. Frequently Asked Questions
What are RP graphite electrodes used for?
RP graphite electrodes are primarily used in electric arc furnaces for melting scrap steel and in the production of ferroalloys and non-ferrous metals.
How do RP graphite electrodes compare to other electrodes?
RP graphite electrodes offer superior conductivity, thermal stability, and chemical resistance compared to other types of electrodes, making them a preferred choice in many metallurgical applications.
Are RP graphite electrodes environmentally friendly?
Yes, RP graphite electrodes are considered environmentally friendly due to their lower carbon footprint and recyclability.
What trends are shaping the future of RP graphite electrodes?
Technological innovations, sustainability initiatives, and customization for specific industries are key trends shaping the future of RP graphite electrodes.
What challenges does the RP graphite electrode industry face?
Challenges include supply chain issues, technological adaptation, and market competition, which can impact production and profitability.
9. Conclusion
RP graphite electrodes are transforming the metallurgical industry, offering enhanced efficiency, sustainability, and versatility. As we look towards the future, their role will only become more significant, driven by technological advancements and a growing emphasis on eco-friendly practices. By addressing the challenges faced by the industry, RP graphite electrodes will continue to be at the forefront of metallurgical innovation, shaping a more sustainable and efficient future in metal production. Embracing these advancements will not only enhance operational effectiveness but also contribute to a greener planet, ensuring that the metallurgical industries remain resilient and progressive in an ever-changing landscape.
Focus On Hot Spots
The Critical Role of UHP Graphite Electrodes in Minimizing Production Costs
The Critical Role of UHP Graphite Electrodes in Minimizing Production Costs
Table of Contents
1. Introduction to UHP Graphite Electrodes
2. Understanding UHP Graphite Electrodes
3. The Manufacturing Process of UHP Graphite Electrodes
4. Applications of UHP Graphite Electrodes in Industry
5. The Impact of UHP Graphite Electrodes on Production Costs
6. Benefits of Using UHP
Understanding HP Graphite Electrode: Essential Insights for the Metallurgical Industry
HP graphite electrodes play a crucial role in the metallurgical and energy sectors, particularly in the production of steel and other metals through electric arc furnaces (EAFs). These electrodes are made from high-purity petroleum or needle coke, which is then processed to create a material with excellent electrical conductivity and thermal resistance. This unique combination of properties makes