The Critical Role of UHP Graphite Electrodes in Minimizing Production Costs
Summary:
The Critical Role of UHP Graphite Electrodes in Minimizing Production Costs
Table of Contents
1. Introduction to UHP Graphite Electrodes
2. Understanding UHP Graphite Electrodes
3. The Manufacturing Process of UHP Graphite Electrodes
4. Applications of UHP Graphite Electrodes in Industry
5. The Impact of UHP Graphite Electrodes on Production Costs
6. Benefits of Using UHP
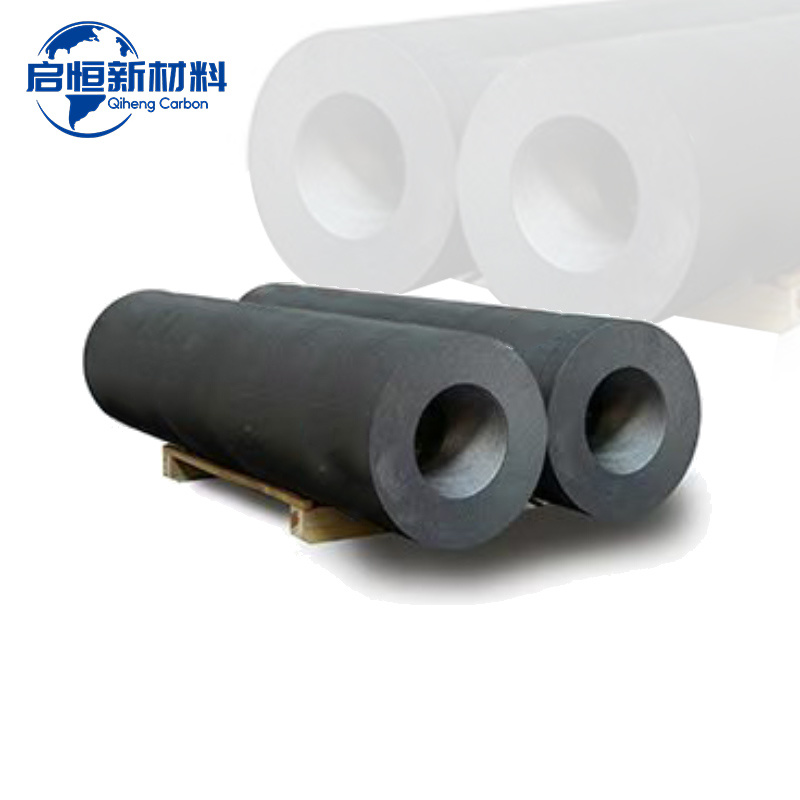
The Critical Role of UHP Graphite Electrodes in Minimizing Production Costs
Table of Contents
- 1. Introduction to UHP Graphite Electrodes
- 2. Understanding UHP Graphite Electrodes
- 3. The Manufacturing Process of UHP Graphite Electrodes
- 4. Applications of UHP Graphite Electrodes in Industry
- 5. The Impact of UHP Graphite Electrodes on Production Costs
- 6. Benefits of Using UHP Graphite Electrodes
- 7. Future Trends in UHP Graphite Electrodes
- 8. Conclusion
- 9. FAQs about UHP Graphite Electrodes
1. Introduction to UHP Graphite Electrodes
UHP (Ultra High Power) graphite electrodes play a pivotal role in the electrical steelmaking and foundry industries. By conducting electricity at high temperatures, they facilitate efficient melting processes in electric arc furnaces (EAFs). The significance of UHP graphite electrodes extends beyond their technical capabilities; they are crucial in maintaining and optimizing production costs. This article delves into the manufacturing processes, applications, and the profound impact of UHP graphite electrodes on production expenses.
2. Understanding UHP Graphite Electrodes
UHP graphite electrodes are characterized by their exceptional electrical conductivity, high thermal resistance, and mechanical strength. These electrodes are manufactured from petroleum coke and needle coke, which undergo various processes, including mixing, molding, baking, and graphitization. UHP graphite electrodes differ from standard electrodes in their capacity to withstand greater electrical current levels, making them suitable for high-demand applications.
2.1 Properties of UHP Graphite Electrodes
The primary properties that define UHP graphite electrodes include:
- **High Electrical Conductivity**: Essential for efficient electric arc melting.
- **Superior Thermal Resistance**: Allows for operation in extreme heat settings.
- **Mechanical Strength**: Ensures durability and longevity during use.
2.2 Types of UHP Graphite Electrodes
Various types of UHP graphite electrodes cater to specific industrial requirements:
- **UHP Round Electrodes**: Commonly used in EAFs.
- **UHP Square Electrodes**: Often used in foundries and other melting applications.
3. The Manufacturing Process of UHP Graphite Electrodes
The production of UHP graphite electrodes is a meticulous process that involves several steps to ensure high-quality output. Understanding this process is crucial for appreciating their impact on production costs.
3.1 Raw Material Selection
The quality of raw materials, primarily petroleum and needle coke, directly affects the performance of the electrodes. The selection is critical in ensuring optimal conductivity and strength.
3.2 Mixing and Molding
The raw materials are mixed with a binding agent to create a paste, which is then molded into the desired shape. This stage determines the final structure of the electrodes.
3.3 Baking
After molding, the electrodes undergo baking at high temperatures. This process is vital for hardening the material and enhancing its properties.
3.4 Graphitization
The final stage involves graphitization, where electrodes are subjected to even higher temperatures to convert them into graphite, significantly improving their conductivity and thermal resistance.
4. Applications of UHP Graphite Electrodes in Industry
UHP graphite electrodes are utilized across various industries, primarily in:
- **Steelmaking**: In electric arc furnaces, they are crucial for melting scrap steel and producing high-quality steel.
- **Foundries**: Used for melting non-ferrous metals and alloys.
- **Manufacturing of Silicon**: Essential in the production of silicon for solar panels and semiconductors.
4.1 Role in Electric Arc Furnaces
In electric arc furnaces, UHP graphite electrodes are indispensable. They facilitate the melting process by generating high temperatures through electric arcs, enabling the transformation of raw materials into molten metal.
5. The Impact of UHP Graphite Electrodes on Production Costs
Understanding the connection between UHP graphite electrodes and production costs is vital for industries seeking to improve efficiency and reduce expenses.
5.1 Efficiency Enhancements
The use of UHP graphite electrodes improves the overall efficiency of production processes. They enable faster melting times and reduce energy consumption, directly impacting cost savings.
5.2 Cost Analysis
While the initial investment in high-quality UHP graphite electrodes may be significant, their durability and efficiency lead to lower operational costs in the long run. Companies can achieve substantial savings by optimizing their production processes.
5.3 Reducing Waste and Scrap Rates
The high performance of UHP graphite electrodes reduces the likelihood of defects and waste during the melting process, further contributing to cost reduction.
6. Benefits of Using UHP Graphite Electrodes
Utilizing UHP graphite electrodes offers several advantages:
- **Enhanced Production Efficiency**: Less downtime due to electrode failure.
- **Improved Quality of End Products**: Higher purity levels in melted materials.
- **Lower Energy Consumption**: Direct correlation to reduced production costs.
6.1 Long-term Cost Savings
Investing in UHP graphite electrodes can yield long-term benefits. Their longevity and reduced maintenance needs translate into lower operational costs, making them a wise choice for manufacturers.
7. Future Trends in UHP Graphite Electrodes
As industries evolve, so does the technology behind UHP graphite electrodes. Emerging trends to consider include:
- **Increased Demand for Eco-Friendly Products**: A shift towards sustainable materials in electrode manufacturing.
- **Technological Advancements**: Innovations in electrode design and production techniques to enhance performance and reduce costs.
7.1 Sustainability Initiatives
With rising environmental concerns, the industry is focusing on sustainable practices. The development of electrodes from recycled materials is gaining traction, promising a reduced environmental footprint.
7.2 Innovations in Production Techniques
Advancements in manufacturing processes can lead to improvements in the quality and performance of UHP graphite electrodes, further lowering production costs.
8. Conclusion
UHP graphite electrodes are integral to the metallurgical and energy sectors, offering significant benefits in production efficiency, quality, and cost reduction. Their role in electric arc furnaces and other applications underscores their importance in modern manufacturing processes. As industries continue to evolve and seek cost-effective solutions, the demand for UHP graphite electrodes will undoubtedly grow, paving the way for innovations that enhance their performance and sustainability.
9. FAQs about UHP Graphite Electrodes
9.1 What are UHP graphite electrodes?
UHP graphite electrodes are specialized electrodes with high electrical conductivity and thermal resistance, used mainly in electric arc furnaces for steel and metal production.
9.2 How do UHP graphite electrodes reduce production costs?
They minimize energy consumption, enhance melting efficiency, and decrease scrap rates, leading to significant cost savings in production.
9.3 What industries primarily use UHP graphite electrodes?
They are mainly used in steelmaking, foundries, and the manufacturing of silicon for various applications.
9.4 Are there environmental considerations with UHP graphite electrodes?
Yes, there is a growing focus on sustainable practices in the production of UHP graphite electrodes, including the use of recycled materials.
9.5 How does the quality of UHP graphite electrodes affect production?
Higher quality electrodes lead to better conductivity and thermal resistance, resulting in improved production efficiency and lower operational costs.
Previous:
Focus On Hot Spots
The Critical Role of UHP Graphite Electrodes in Minimizing Production Costs
The Critical Role of UHP Graphite Electrodes in Minimizing Production Costs
Table of Contents
1. Introduction to UHP Graphite Electrodes
2. Understanding UHP Graphite Electrodes
3. The Manufacturing Process of UHP Graphite Electrodes
4. Applications of UHP Graphite Electrodes in Industry
5. The Impact of UHP Graphite Electrodes on Production Costs
6. Benefits of Using UHP
Understanding HP Graphite Electrode: Essential Insights for the Metallurgical Industry
HP graphite electrodes play a crucial role in the metallurgical and energy sectors, particularly in the production of steel and other metals through electric arc furnaces (EAFs). These electrodes are made from high-purity petroleum or needle coke, which is then processed to create a material with excellent electrical conductivity and thermal resistance. This unique combination of properties makes