Maximizing Efficiency and Performance: Best Practices for Graphite Electrodes in Electric Arc Furnaces
Summary:
Maximizing Efficiency and Performance: Best Practices for Graphite Electrodes in Electric Arc Furnaces
Table of Contents
1. Introduction to Graphite Electrodes and Electric Arc Furnaces
2. Understanding Graphite Electrodes: Properties and Types
3. The Role of Graphite Electrodes in Electric Arc Furnaces
4. Best Practices for Using Graphite Electrodes
4.1 Selec
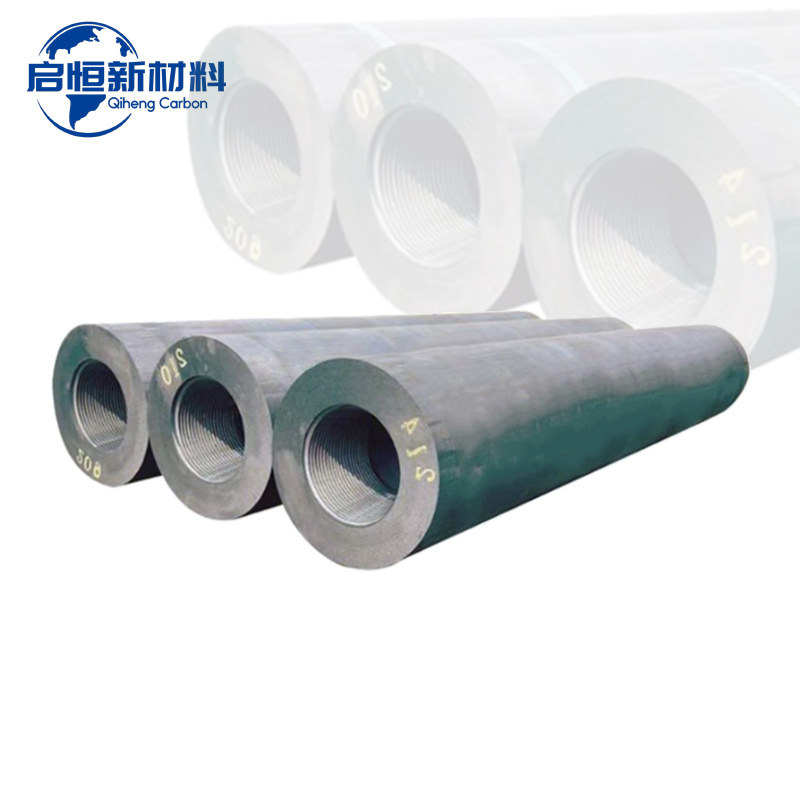
Maximizing Efficiency and Performance: Best Practices for Graphite Electrodes in Electric Arc Furnaces
Table of Contents
- 1. Introduction to Graphite Electrodes and Electric Arc Furnaces
- 2. Understanding Graphite Electrodes: Properties and Types
- 3. The Role of Graphite Electrodes in Electric Arc Furnaces
- 4. Best Practices for Using Graphite Electrodes
- 4.1 Selection Criteria for Graphite Electrodes
- 4.2 Operational Techniques for Enhanced Performance
- 4.3 Maintenance Procedures for Longevity
- 5. Troubleshooting Common Issues with Graphite Electrodes
- 6. Sustainable Practices in the Use of Graphite Electrodes
- 7. Future Trends in Graphite Electrodes for Electric Arc Furnaces
- 8. Conclusion
- 9. FAQs
1. Introduction to Graphite Electrodes and Electric Arc Furnaces
Graphite electrodes play a pivotal role in the operation of electric arc furnaces (EAFs), which are crucial in steelmaking and other metallurgical processes. The efficiency and effectiveness of EAFs largely depend on the quality and performance of the graphite electrodes used. In this article, we will explore the best practices to maximize the efficacy of graphite electrodes in EAF operations, ensuring optimal energy consumption and output quality.
2. Understanding Graphite Electrodes: Properties and Types
Graphite electrodes are made from high-quality petroleum and needle coke, which undergoes a process of graphitization. This process enhances their conductivity and mechanical strength. There are various types of graphite electrodes, including:
2.1 Types of Graphite Electrodes
- **Regular Power Electrodes**: Standard-grade electrodes that cater to general applications.
- **High Power Electrodes**: Designed for high-current applications, offering enhanced durability.
- **Ultra High Power Electrodes**: Provide superior performance for intensive EAF operations, minimizing electrode wear.
Each type serves specific operational needs, and selecting the right one is crucial for optimal performance.
3. The Role of Graphite Electrodes in Electric Arc Furnaces
The primary function of graphite electrodes in EAFs is to conduct electricity to the charge materials, creating an electric arc that generates heat. This process melts scrap metal and other materials, enabling the production of high-quality steel. The performance of the electrode directly impacts the furnace's energy efficiency, melting capacity, and overall productivity.
4. Best Practices for Using Graphite Electrodes
To ensure that graphite electrodes perform at their best, adhering to best practices is essential.
4.1 Selection Criteria for Graphite Electrodes
Choosing the right graphite electrode is fundamental for effective EAF operation. Consider the following criteria when making your selection:
- **Current Rating**: Ensure the electrode can handle the required amperage.
- **Resistivity**: Lower resistivity results in better conductivity and reduces power consumption.
- **Mechanical Strength**: Select electrodes with high tensile strength to withstand operational stresses.
4.2 Operational Techniques for Enhanced Performance
To maximize the lifespan and efficiency of graphite electrodes, implement these operational techniques:
- **Optimal Power Input**: Adjusting the power input to match the operational requirements prevents overheating and premature wear.
- **Electrode Positioning**: Proper positioning within the EAF ensures even arc formation and minimizes local wear.
- **Uniform Mixing of Charge Materials**: Ensuring that scrap metal and additives are evenly mixed leads to balanced heating and reduces electrode consumption.
4.3 Maintenance Procedures for Longevity
Regular maintenance is vital for extending the life of graphite electrodes. Key procedures include:
- **Monitoring Wear Rates**: Keep track of electrode consumption rates to anticipate replacements.
- **Cleaning**: Removing residue from electrodes prevents conductivity issues.
- **Inspection**: Regularly inspect electrodes for cracks or damage that may affect performance.
5. Troubleshooting Common Issues with Graphite Electrodes
Encountering problems with graphite electrodes is common in EAF operations. Here are some frequent issues and their solutions:
- **Electrode Breakage**: Caused by excessive thermal stress; ensure uniform thermal distribution.
- **Increased Power Consumption**: Often results from improper electrode positioning or wear; adjust input power and replace worn electrodes promptly.
- **Poor Melting Efficiency**: Can stem from low-quality electrodes; switch to higher-grade electrodes for better performance.
6. Sustainable Practices in the Use of Graphite Electrodes
Sustainability is increasingly important in the metallurgical industry. Implementing the following practices helps minimize environmental impact:
- **Recycling**: Reusing graphite electrodes reduces waste and lowers production costs.
- **Energy Efficiency**: Utilizing high-quality electrodes maximizes energy consumption, contributing to a lower carbon footprint.
- **Alternative Materials**: Research into alternative materials can reduce reliance on traditional graphite sources, promoting sustainability in the industry.
7. Future Trends in Graphite Electrodes for Electric Arc Furnaces
The landscape of graphite electrodes is evolving. Emerging trends include:
- **Innovative Materials**: Research is underway to develop synthetic alternatives to traditional graphite, potentially offering enhanced performance.
- **Smart Technology Integration**: The implementation of IoT and AI in EAF operations can optimize electrode usage and maintenance scheduling.
- **Sustainability Innovations**: Continuous efforts to improve the recyclability and environmental impact of graphite electrodes will shape the future of EAF technology.
8. Conclusion
In conclusion, the effective use of graphite electrodes in electric arc furnaces is crucial for optimizing performance and efficiency in metallurgical operations. By implementing best practices in selection, operation, and maintenance, industries can significantly enhance their productivity while reducing environmental impact. As the sector evolves, staying informed about emerging trends and sustainable practices will empower businesses to thrive in an increasingly competitive landscape.
9. FAQs
What are graphite electrodes made of?
Graphite electrodes are primarily composed of petroleum and needle coke, which are subjected to a graphitization process.
How do I choose the right graphite electrode?
Consider factors like current rating, resistivity, and mechanical strength when selecting graphite electrodes for your EAF operations.
What issues can arise with graphite electrodes?
Common issues include electrode breakage, increased power consumption, and poor melting efficiency.
How can I extend the life of my graphite electrodes?
Regular monitoring, cleaning, and inspection of electrodes can significantly prolong their lifespan.
What are the sustainability practices related to graphite electrodes?
Practices include recycling, energy efficiency measures, and exploring alternative materials to reduce environmental impact.
By prioritizing these best practices and staying proactive about maintenance, graphite electrodes can be leveraged to their fullest potential, ensuring efficient and sustainable operations in electric arc furnaces.
Focus On Hot Spots
Understanding High Power Graphite Electrode: A Key Component in Metallurgical Industries
High power graphite electrodes (HPGE) play a crucial role in various metallurgical processes, particularly in electric arc furnaces (EAF) used for steel manufacturing and other metal recycling operations. Their ability to withstand high temperatures and conductive properties makes them indispensable in these applications. As industries strive for efficiency and sustainability, understanding the te
Maximizing Efficiency and Performance: Best Practices for Graphite Electrodes in Electric Arc Furnaces
Table of Contents
1. Introduction to Graphite Electrodes and Electric Arc Furnaces
2. Understanding Graphite Electrodes: Properties and Types
3. The Role of Graphite Electrodes in Electric Arc Furnaces
4. Best Practices for Using Graphite Electrodes
4.1 Selec